Opening Success: Casting Aluminum Made Easy
Opening Success: Casting Aluminum Made Easy
Blog Article
Aluminum Casting Services Introduced: Necessary Insights and Tips
Checking out the realm of light weight aluminum spreading services can unveil a world of complex processes and nuanced factors to consider that are important for effective results. As markets significantly transform to light weight aluminum for its light-weight yet resilient properties, comprehending the essentials of casting ends up being vital. From the fundamental methods to the intricate details that can make or damage a casting job, there is a riches of insights and tips waiting to be found. As we venture into the realm of aluminum spreading services, prepare to reveal the essential components that can form the trajectory of your projects and raise your understanding of this intricate craft.
The Basics of Aluminum Spreading
What basic processes are included in light weight aluminum casting that develop the foundation of this commonly used manufacturing method? Light weight aluminum spreading is a versatile and cost-effective approach used in various sectors to develop complicated and elaborate metal parts.
After solidification, the mold is removed, and the casting goes through ending up procedures such as warmth machining, therapy, and surface area layer to meet the needed requirements. Understanding these essential procedures is vital for achieving top quality light weight aluminum spreadings with mechanical homes and accurate dimensions.
Different Casting Methods Discussed
Checking out the various techniques used in aluminum spreading supplies important insights right into the diverse techniques used to achieve precise and detailed metal parts. One common method is sand spreading, where a mold and mildew is developed utilizing compacted sand around a pattern of the desired component. This method is versatile and economical, appropriate for both straightforward and complex shapes. Another technique, pass away spreading, includes injecting molten aluminum right into a steel mold and mildew under high stress. Die casting allows high precision and repeatability, making it optimal for mass production of small to medium-sized components. For even more intricate designs, financial investment casting is often preferred. This approach makes use of wax patterns that are thawed away, leaving a dental caries for the molten light weight aluminum to fill up. Financial investment spreading yields precise information and smooth coatings, making it prominent in industries like aerospace and auto. Each spreading technique has its distinct benefits and is selected based upon factors such as complexity, expense, and quantity considerations.
Factors to Take Into Consideration When Selecting a Provider
When picking an aluminum spreading provider, examining their experience and competence is essential for ensuring top quality and dependability in the production procedure. The provider's experience in the area suggests their experience with various spreading methods, possible obstacles, and best methods. It is vital to make inquiries regarding the sorts of tasks they have dealt with in the past, ensuring they line up with the intricacy and requirements of your own project.
Furthermore, consider the copyright's credibility within the sector. Search for testimonials, testimonies, and situation research studies that demonstrate their capacity to supply top visite site quality light weight aluminum castings constantly. A trusted supplier will certainly often have accreditations or affiliations with market organizations, showcasing their dedication to excellence and adherence to industry requirements.
Furthermore, evaluate the copyright's capabilities in regards to modification, quantity needs, and job timelines. Make certain that they can fit your details requirements and have the flexibility to scale production as needed. Efficient communication and transparency relating to costs, lead times, and high quality control procedures are additionally vital elements to think about when selecting a light weight aluminum casting solution supplier.
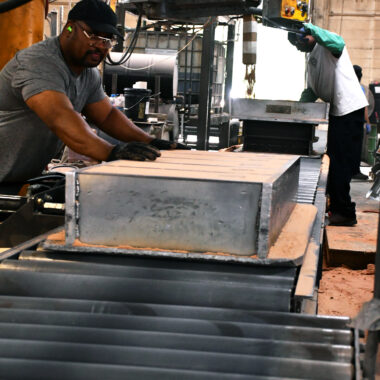
Common Challenges and Solutions
Navigating through the complexities of aluminum casting processes typically offers suppliers with a collection of difficulties that need ingenious options to make sure performance and quality in manufacturing. One typical obstacle dealt with in aluminum casting is the formation of flaws such as porosity, contraction, or incorporations due to inappropriate mold and mildew style or inadequate metal high quality.
One more challenge hinges on attaining precise dimensional precision, specifically for intricate geometries. visit homepage Variants in cooling rates, mold and mildew development, and material homes can result in deviations from the desired dimensions. Implementing advanced modern technologies like computer-aided style (CAD) and computer numerical control (CNC) machining can enhance accuracy and uniformity in aluminum spreading. Furthermore, maintaining appropriate control over the melting and putting procedures is critical to avoid problems like getting too hot or irregular distribution of the molten steel my latest blog post - casting aluminum. By spending in automation and real-time surveillance systems, suppliers can enhance procedure control and lessen variants, ultimately boosting the general high quality of light weight aluminum cast products.
Tips for Optimizing Your Casting Projects
To boost the efficiency and top quality of your light weight aluminum casting jobs, applying calculated optimization strategies is vital. One key pointer for enhancing your casting jobs is to thoroughly make the gating system. By ensuring that the gating system is properly designed and effectively put, you can enhance the flow of molten aluminum and reduce the possibilities of defects in the last casting. In addition, using computer system simulations can help in forecasting and assessing the flow of steel throughout the casting process, permitting for adjustments to be made before actual production begins.
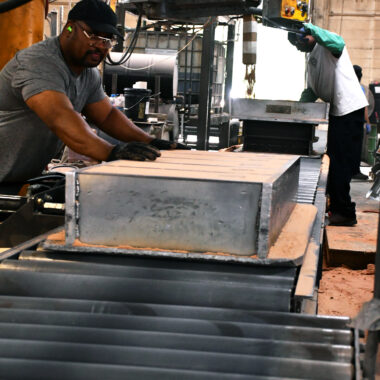
Final Thought
To conclude, understanding the essentials of light weight aluminum spreading, various casting approaches, aspects to think about when picking a company, common difficulties and solutions, and tips for enhancing casting tasks are important for effective end results. By adhering to these insights and applying best people, services and methods can make certain efficient and effective light weight aluminum casting solutions that meet their certain demands and needs.
Recognizing these essential procedures is vital for accomplishing high-quality light weight aluminum spreadings with exact dimensions and mechanical homes.
When selecting a light weight aluminum spreading solution company, examining their experience and knowledge is important for making sure high quality and reliability in the production process. Effective communication and transparency concerning costs, lead times, and high quality control processes are also important elements to consider when picking an aluminum casting solution supplier.
Navigating through the complexities of light weight aluminum spreading processes often presents makers with a series of challenges that require ingenious services to guarantee effectiveness and top quality in manufacturing. One usual challenge faced in aluminum casting is the development of defects such as porosity, shrinkage, or additions due to incorrect mold design or poor metal top quality.
Report this page